FullSTIM: Production and Profitability
- roneill26
- Jun 10
- 4 min read

The Multi-Billion Dollar Problem
Oil producers face a cascade of interconnected challenges that traditional solutions can't solve: production decline, scale buildup, paraffin deposits, reduced flow, and equipment damage. Paraffin deposition problems alone "cost the petroleum industry multiple billions of dollars annually in lost production and maintenance expenses to remove wax deposits in subsurface tubulars" [1]. Paraffin buildup leads to decreased well flow rates and can eventually cause total blockage, while formation damage from heavy organics can contribute to observed permeability reduction and production declines.
The problem with traditional approaches:
Scale inhibitors lose 40-60% effectiveness after six months, creating ongoing costs exceeding $10,000 annually per well (SPE Paper 185638)
Acid treatments can cause 22–35% corrosion rates on equipment (Oil & Gas Journal, 2023). While they may remove immediate scale deposits, they often accelerate corrosion.
Mechanical solutions require 3-7 days of downtime per event and create a 5-8% risk of additional equipment damage during scale removal (SPE Paper 173850)
~10,000 ESP annual pump failures due to scale buildup translating to ~$500mm in direct replacement costs and associated downtime (SPE Paper 113820)
Prior to failure, scale buildup reduces production efficiency by 15-30% (NACE International)
Wells with scale problems require 2-3x more routine maintenance interventions (SPE Paper 187340) which cost $15,000-$30,000 per event depending on well depth and location
Hot oil treatments often become saturated with wax and may exacerbate formation damage and production decline.
FullSTIM: Multi-Dimensional Solutions for Multi-Factor Problems
TenEx Technologies' FullSTIM delivers a fully integrated treatment that addresses major production challenges simultaneously through customized components.
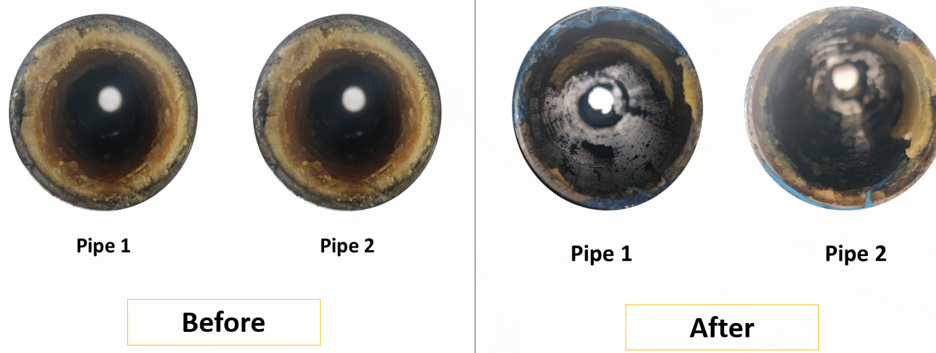
FullSTIM addresses:
Dissolving hard inorganic scale (iron oxides, calcium carbonate, etc.)
Removing and inhibiting organic scale/deposition (paraffin & asphaltene)
Breaking gel/polymers (guar gel, crosslinked-gel, polyacrylamide, xanthan)
Modifying long-term wettability to improve flow characteristics
Enhancing heavy oil mobility for improved production
Providing high salinity foaming agents for multiple applications
4 Key Components
1. CeraFLO™: Advanced Organic Deposit Management
CeraFLO targets organic deposits with multiple custom formulations that provide three key functions:
Dissolving organic deposits including paraffin and asphaltene
Inhibiting future buildup to extend maintenance intervals
Lowering heavy oil viscosity to enhance flow characteristics
Laboratory testing proves CeraFLO's superiority to conventional treatments. While traditional solvents like xylene temporarily dissolve deposits but lead to recrystallization upon cooling, CeraFLO-treated samples show no evidence of recrystallization or deposition under identical conditions.
In extensive testing with high-paraffin content oil (>50%), CeraFLO formulations maintained significantly better oil mobility compared to untreated samples, even after 72 hours at challenging temperatures. This translates directly to sustained production improvements in the field.
At just 0.5 gpt concentration, CF30 achieved a 65% drop in viscosity compared to only 32% for xylene, enabling dramatically improved flow rates and production.

2. TSB Scale Breaker: The Inorganic Scale Solution
TSB addresses inorganic scale while eliminating the hazards of traditional acid treatments:
Non-corrosive formulation protects equipment integrity vs. severe corrosion with traditional acids
Built-in corrosion inhibition extends pump life
Superior dissolution rates:
99% calcite dissolution in one hour
99% dolomite dissolution in one hour
52% barite dissolution in 24 hours

Exceptional penetration:
TSB-1: 50-60% penetration vs. 0-10% penetration with 15% HCl
TSB-2: 80-90% penetration

Permeability restoration:
455% permeability gain after 4 hours
635% permeability gain after 24 hours
3. TGB Gel Breakers: Polymer and Gel Resolution
TGB Gel Breakers address polymer damage that severely restricts flow:
Dissolves all common oilfield polymers (xanthan gum, guar gum, crosslinked gels, HVFR)
Restores permeability in polymer-damaged formations
Works in minutes: crosslinked gels that completely clog equipment flow normally in just 7 seconds after treatment
Prevents formation damage from incomplete gel breaking
4. High Salinity Foaming Agents: Enhanced Recovery Operations
TenEx's foaming agents outperform leading commercial foamers in harsh conditions:
Superior foam stability in high-temperature (160°F) and high-salinity (110,000 ppm TDS) environments
TF-1 and TF-2 maintain foam integrity where competitors fail within hours
Essential for foam diversion, CO2-EOR, and dewatering operations
Proven 6+ hour stability vs. competitor breakdown in 1-3 hours
Synergies of a Multi-Factor Approach
When all four FullSTIM components work together:
CeraFLO exposes inorganic scale for TSB dissolution while dissolving organic deposits
TSB creates clean flow channels for better penetration of other treatments while dissolving inorganic scale
TGB removes polymer barriers that block other chemical treatments from reaching target zones
Foaming agents enhance placement and contact time of active ingredients in target zones
Combined treatment prevents future deposition
FullSTIM: Customized Solutions for Custom Problems
TenEx's approach begins with rigorous analysis to create targeted treatment plans customized to each well's unique challenges:
Diagnostic Analysis: Clients send downhole pump scale samples for comprehensive testing. TenEx analyzes the specific chemical composition of the scale, which can vary significantly from well to well and field to field.
Customized Testing: TenEx conducts systematic testing on scale samples with various CeraFLO formulas and TSB combinations to identify the optimal treatment for the specific well conditions, ensuring maximum effectiveness for each unique situation.
Proven Field Results
Case Study #1: Production Stabilization
Results after 5 months:
Production decline reversed
Water production decreased 38-60%
Pump RPM requirements reduced 22%


Case Study #2

The Economic Advantage
FullSTIM delivers superior results at lower total cost:
Longer-lasting treatment effects
Extended equipment life
Enhanced production
Simplified operations
Eliminated polymer damage costs and recompletion expenses
Reduced foam treatment frequency in EOR operations
Prevention of multiple failure modes simultaneously
Transform Your Well Economics Today
Don't let scale and paraffin issues drain your profits. FullSTIM provides the integrated solution that addresses root causes simultaneously, delivering:
✓ Maximum production from existing wells
✓ Significantly extended equipment life
✓ Reduced intervention frequency and costs
✓ Superior return on investment
Contact TenEx Technologies:
Email: sales@tenextechnologies.com
Website: www.PumpMoreOil.com
References
[1] FQE Chemicals. (2020). "Paraffin Deposition Theory and Control Through Chemistries." Available at: https://fqechemicals.com/paraffin-deposition-theory/